Coir machine that takes on 1000 husks an hour
From coconut thief traps to coconut husking machines, inventing a range of useful apparatus is almost second nature to Dhammika, whose creative prowess goes back to his childhood.
Now, having invented a Coir machine, which earned him the Presidential Award 2007 and 2008, the World Intellectual Property Organization (WIPO) award 2009, the INNOMECH University of Moratuwa 2009 and the Rajatha Sammanaya 2009, Ratnayake Mudiyanselage Dhammika is one of the nominees for the inaugural ‘The Ray’ award which will be announced on October 17.
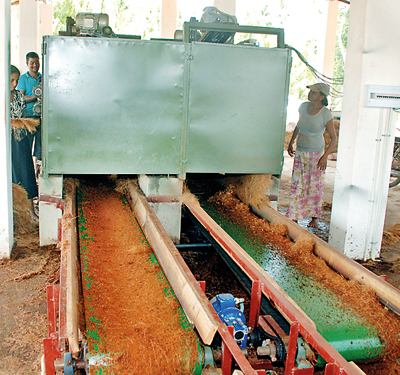
The efficient coir machine. Pic by M.D. Nissanka
Though Dhammika’s education was cut short at the A’ Levels, he has proved that ‘out of the box’ thinking coupled with perseverance can achieve much. Having acquired the skills needed to become a technician, he has continued in this trade, sharpening his wits in the field of inventing.
“It is my passion to complete whatever creation I get my hands on to,” says Dhammika.It is this passion and fierce determination, that spurred him on with his invention of the efficient Coir machine, despite discouragement at various points.
“I came up with the idea to develop a foolproof coir mill after seeing the inefficiencies of the current machines as well as the safety concerns they pose,” explains Dhammika, adding that many attempts have been made to come up with a safe and efficient machine since 1932.
In 2000, Dhammika made his first coir machine amalgamating many little parts and spent four years finetuning it. Currently, 12 of his machines are in operation around the country. Here’s how it works:
The coconut husk is fed into the machine by hand and two chains work on it, removing the outer covering and revealing the fibre. The fibre is then fed into a wheel drum that refines the fibres which are re-fed into a compartment that binds 12 fibre piles together, to produce the bristle fibres. The fibre dust that is produced in the process is given out through another conveyor and collected separately.
“This machine requires only four unskilled workers to perform a task that previously needed 12 highly skilled workers,” says Dhammika.
While the traditional method involved women holding the husk down into the feeder connected to large spike drums, here it is just placed on a conveyor.
1000 coconut husks are worked on per hour, in contrast to the previous rate of only 200 peels per hour. From an input of 1000 husks, 65 kg of Bristle fibre (highest rate recorded), 120 kg of mattress fibre, and 210 kg of dust can be obtained.
There are a wide range of products that can be made from the three different grades of coconut fibre. The previous machines could not separate the coconut fibre into different grades unlike Dhammika’s coir mill.
While in general there is a high demand for the coconut fibre, mattress and dust (kohubath) that is produced through the process, it is the bristle fibre which is in high demand.
Dhammika says that he spent approximately Rs 10 million developing and producing his machines. They cost 28 lakhs to instal and with added maintenance, the total cost amounts to approximately Rs 40 lakhs.
“However, a net profit of six lakhs per month can be guaranteed,” says Dhammika confidently, adding that he took a loan of Rs 47 lakhs for this purpose and was able to pay it off within seven months as the output was so high.
“Any invention should give focus to the profit that it will ultimately yield, while serving a rightful purpose in the community,” says Dhammika.
Looking into the three I’s
Of the 94 Presidential Award winners, 56 sent in their applications, of which 17 were long-listed. The 17 long-listed candidates were then interviewed by the panel of judges and six nominees were shortlisted. “We chose the winner based on three main criteria,” says the Chairperson of the panel of judges, of ‘The Ray’ award, Prof. Uditha Liyanage.
He explained that firstly, they looked for the idea and the unique thinking or the ‘wow factor’ behind the creation. Secondly, the innovation or stage of development was considered.
Here, the judges looked at how far the idea had evolved from a concept to reality and whether it has been converted to a product or service. More marks were awarded to those who had come closer to commercializing the product or service.
Finally, the socio-economic impact, the question of whether the invention solves a problem and to what extent the problem is solved were considered.
“Basically we looked at three ‘I’s – Invention, Innovation and Impact,” Prof. Liyanage summed up
The winner will be announced at the Ray award ceremony on October 17.
“The Ray”: Paving the way for another Ray
“The Ray’ awards will be held on October 17 at the Oak Room of the Cinnamon Grand hotel honouring the genius and vision of the man after whom it is named. From aeronautical, mechanical and agricultural engineering to renewable energy technologies to competing in the Olympics to being an accomplished violinist and oil painter, Dr. Philip Revatha (Ray) Wijewardene was a unique personality. He pioneered the world’s first two wheeled tractor – the Landmaster in 1955, which in the years that followed sold over 300,000 units in 27 countries. His engineering genius apart he was also an aeronautical buff- building as well as flying ultra-light aircraft and helicopters.
In recognition of his distinguished service to his country, the government of Sri Lanka awarded him the highest national honours of Vidya Jyothi and Deshamanya.
In 2011, the Ray Wijewardene Charitable Trust (RWCT) was established to promote and sustain the vision and ideas of Ray Wijewardene. As part of its activities, the RWCT decided to initiate ‘The Ray’ award, as a means of encouraging on-going innovation and enterprise in areas of public interest and continuing his vision of innovation. ‘The Ray’ award is presented by the RWCT in collaboration with the Sri Lanka Inventors Commission and the Commercial Bank.
“We wanted to create another Ray and hence the award was named ‘The Ray’,” explained one of the Founder Trustees of the RWCT, Professor Malik Ranasinghe.
The Presidential Award winners of the Sri Lanka Inventors Commission were invited to apply for this award, which will be a biennial award. As it is a lifetime award, those who applied for the award but did not win it, can apply again after further improving and developing their invention.
“An idea has to go through the stages of invention, innovation and commercialization,” said Prof. Ranasinghe adding that many of the inventors in Sri Lanka are unable to follow this process as they lack the necessary know-how and resources.
The Commercial Bank will provide a credit line of Rs. one million to the winner.
The bank will hold the money for the winner, releasing the necessary amount as per the inventor’s requirement as he develops and commercializes his invention. The University of Moratuwa would provide the technical support needed to convert the winner’s invention to a product or process ready for the market.
“Emphasis is laid on how far the invention can be commercialized,” says Prof. Ranasinghe.
Follow @timesonlinelk
comments powered by Disqus