Shape of things to come
It took Nissanga Warnapura 48 hours to print his first hand. Built for a little nine-year-old girl who lost her fingers and a part of her wrist to amniotic band syndrome, this prototype is made of plastic and nylon thread and consists of 54 parts. It looks uncomfortably geometric, its plastic skeleton all white and stiff, but the ‘fingers’ clench as the wrist flexes, allowing the wearer to hold things and even grip an object lightly. There’s much work ahead – it may take as many as 10 more prototypes to perfect. It still won’t be pretty but it may just transform her life.
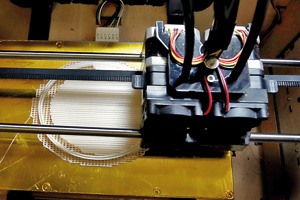
Pic by M. A. Pushpa Kumara
Working this miracle in plastic are three 3D printers, housed in a little spare room in Nissanga’s home. Keeping it small and one-man strong is a part of the “zero-overhead” policy which has allowed this exciting new business to cater to all sorts of clientele. There are the parents buying plain white minions and the girlfriends who buy mini-renditions of classic cars – both also purchase boxes of acrylic paint, so the lucky recipient can have fun painting their own model. There are the engineers ordering spare parts, mounts and containers of every description; there are the aerial enthusiasts who are excited by affordable quad-copter mounts, and artists who leave the actual sculpting to the machine. Toy makers are customising doll heads, devotees are ordering statues of Ganesh (complete with iPad docks), sports fans are taking home unique memorabilia, architects want models of their buildings and young lovers are collecting perfect roses that will bloom for years to come.
The demand seems to have taken this little enterprise by surprise – and they’ve only been in business for a few months. The 3D Concept Studio began with just one printer and when we step in to the tiny room, it’s to find this workhorse humming away. The first element is the actual 3D design, most of which comes from the 3D Design Studio.
The actual building takes place on a heated plate that allows the plastic to bond to its surface as the machine begins laying the foundations of a container. It’s a slow, almost hypnotic process to watch. Peek behind the contraption and you’ll see the reels containing what appears to be a thick plastic string in a dazzling array of colours (white, red, blue, orange, green, black and even silver and gold.) Passed through the machine, the now melted substance is fuelled through a slender nozzle. Pouring out in a consistency not unlike toothpaste, it can replicate the most intricate of shapes, painstaking layer by layer.
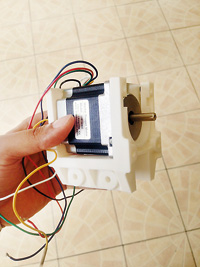
A 3D printed mount
For designers, artists and engineers, 3D printing offers exciting possibilities. It’s a quick way to test a design or a new mould, offering not just ease but also considerable savings. The last element isn’t a coincidence. The cost of 3D printing can be much higher when businesses who’ve invested in $30,000 – $40,000 machines must recoup their investment. However, when setting up shop in Sri Lanka, 3D Concept Studio opted to set up their own rig with parts imported for different countries – the frame from China, the nozzle from the U.S. Now, they charge upwards of just Rs1500 for an object. They’ve already generated a lot of local buzz with interactive workshops that served as an introduction to what these machines could accomplish. Working closely with the likes of the University of Moratuwa, the goal is to contribute to a boom in innovation.
While it might make more sense for individual customers to drop in with their requests, the studio also offers machines for rent as well as purchase.
Projects like the prosthetic hand require that experts from multiple fields such as industrial design and medicine to collaborate to create the best product. In this case, the original 3D design was provided by the Australian outfit Robohand but it may be cheaper to actually manufacture it in Sri Lanka, making this the most appealing destination for philanthropists hoping to distribute it globally to those in need.
This is an exciting venture on so many levels – an instance where technology fuels and supports not just industry, innovation and design but promises the opportunity to uplift individuals and empower communities. Find 3D Concept Studio online at: https://www.facebook.com/3dconceptstudioSL