Dankotuwa – transforming the essence of porcelain
DANKOTUWA – The raw smell of porcelain mix wafts some yards away from the Dankotuwa Porcelain PLC (DPL) factory at Dankotuwa, in the North Western Province.

Looks like a dining table! An assembly line at DPL. Pix by Indika Handuwala
Entering the premises, 20 acres in all – the surroundings are impeccable and 5S workplace organisation method that uses a list of five Japanese words:seiri, seiton, seiso, seiketsu, and shitsuke are written in pillars of the building, reinforcing the commitment to perfection.
DPL the earliest to implement 5S as far back as 1992, is also one of the first to implement Kaizen, which is the methodology that promotes the sustainable continuous improvement as a daily way of life for every member within the organization said, Sarath Mallawarachchi, the DPL CEO, opening the door of the ‘mixing’ department to the Business Times team. What strikes us most upon entering this department is that females are in a white dress and males are dressed in black
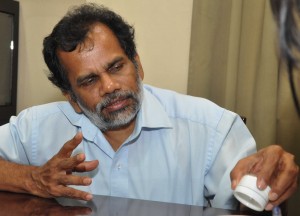
Sarath Mallawarachchi
pants and a white shirt. Mr. Mallawarachchi says that this is the uniform for the factory staff.
The purpose of mixing is to combine the constituents of a ceramic powder to produce a more chemically and physically homogenous material for forming.
Pug mills often are used for mixing ceramic materials. Several processing aids may be added to the ceramic mix during the mixing stage, Mr. Mallawarachchi says, adding that more than 15 different ingredients are used for mixing.
Next is the forming step where dry powders, plastic bodies, pastes, or slurries are consolidated and molded to produce a cohesive body of the desired shape and size. The forms are pink in colour – bowls, tea sets, dishes, etc and the ultimate finished product is the white ware, Mr. Mallawarachchi explains. After forming, ceramics must be dried. “Drying must be carefully controlled to strike a balance between

Fine art
minimising drying time avoiding differential shrinkage, warping, and distortion. The most commonly used method of drying ceramics is by convection, in which heated air is circulated around the ceramics.” Air drying often is performed in tunnel kilns, which typically use heat recovered from the cooling zone of the kiln.
Mr. Mallawarachchi shows a state of the art firing kiln and the area around it is quite warm, as it was in operation at the time.
Prior to firing, which comes next, ceramics often are heat-treated at temperatures well below firing temperatures. The purpose of this thermal processing is to provide additional drying, to vaporize or decompose organic additives and other impurities, and to remove residual, crystalline, and chemically bound water, according to Mr. Mallawarachchi.
For traditional ceramics, glaze coatings often are applied to ceramic ware prior to sintering. Some of the more commonly used raw materials for glazes are quartz, feldspars, carbonates, borates, and zircon which is done at the ‘Glazing’ department.
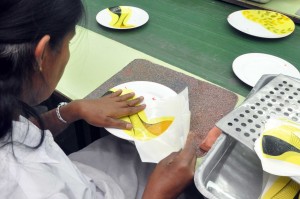
Production process
Firing is the process by which ceramics are thermally consolidated into a dense, cohesive body comprised of fine, uniform grains. “In general ceramics with fine particle size fire quickly and require lower firing temperatures,”
Mr. Mallawarachchi says, adding that parameters that affect firing include firing temperature, time, pressure, and atmosphere.
Following firing, some ceramic products are processed further to enhance their characteristics or to meet dimensional tolerances. In addition, surface coatings are applied to many fired ceramics. The steady hands of employees applying the coatings are truly a treat to watch. What is more mesmerizing is the speed in which they do it and the care in which they handle the delicate products. It truly is brilliance in artistry which translates into contemporary design.
Mr. Mallawarachchi says that surface coatings are applied to traditional clay ceramics to create a stronger, impermeable surface and for decoration. Coatings can be applied dry, as slurries, by spraying, or by vapor deposition.
Originated as a public enterprise in 1984, the company was privatized in 1990 with Japanese shareholders coming in and listed in 1995. Now a public listed company with 4,500 shareholders, it is majority owned by the Lanka Century Investments LCI (formerly ERI) Group. With 1050 staff strength, the factory has many different departments and equally different shifts, which sees a production capacity is 750,000 pieces per month. With a market capitalization of Rs 4.9 billion, DPL exports to 25 countries and 80 per cent of its products are for exports.
“We’re one of the earliest to implement “Quality Week/Month” and the first to introduce automatic pressure casting,” Mr. Mallawarachchi says. DPL products have a very high whiteness – in fact Mr. Mallawarachchi says it’s one of the worlds’ highest. “It has very high translucency and very high thermal shock resistance,” he says, adding that their tableware is food safe conforming to US (Food and Drug Administration) FDA standards.
DPL also uses 24 carat gold and high quality platinum for its gold and silver decorations. “In white porcelain we produce 655,000 pieces, and in ivory porcelain we produce 45,000 pieces.” The total decoration output is 600,000 pieces.
Dankotuwa Porcelain is one of the leading producers of white porcelain finished with gold and platinum designs, Mr. Mallawarachchi says proudly handing a white rice bowl to the Business Times team to inspect. We are speechless as we stare at the translucent exquisiteness of the white masterpiece.