Lessons of co-existence between a Sri Lankan village and a fabric manufacturer
Narthupane Estate, NEBODA – It sounds like a script for a Sri Lankan movie or a television-drama series.
A factory, once the economic centre for the village, collapses over a range of problems including the inability of the management to co-exist with the villages and allegations that factory waste is being dumped in a nearby river, the lifeblood of the community.
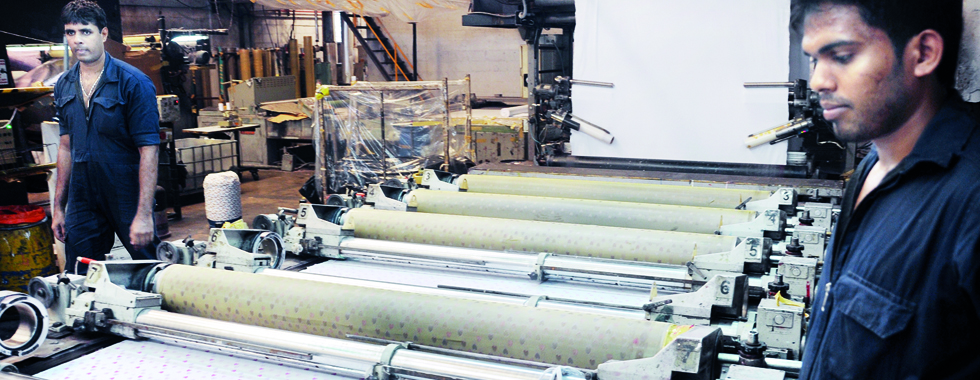
Fabric printing. Pix by Amila Gamage
‘Opinion makers’ from the village take over, unions create issues and the production facility is in tatters. In walks a trouble-shooter with a daunting task – turn around the factory or …. Within months, the management and the village learn to co-exist and the factory in back on track. Everyone is happy. The river flows smoothly.
Sounds familiar? The remarkable turnaround sequence at the loss-making Hayleys MGT Knitting Mills Plc at Narthupana Estate, Neboda in the Kalutara district is probably one among quite a few turnaround successes in Sri Lanka that hasn’t received sufficient public attention.
The secret ingredient: co-existence of the village and an ‘alien’ factory. Another lesson is that workplace jobs must go to villagers first before bringing in others. Corporate social responsibility, a buzzword in Sri Lanka’s private sector, must start at home – caring for workers, their families and their environment.
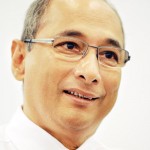
Rohan Goonetilleke
That’s what paid off at this Hayleys facility which is about 60 km south of Colombo, and, leading the turnaround charge was company Managing Director Rohan Goonetilleke, no stranger to reviving loss-making firms having faced a similar situation at Textured Jersey, another well-known fabric manufacturer.
When he first moved in two years ago, Mr. Goonetilleke recalls: “There was chaos at the factory. There were no links with the village. Residents accused the factory of dumping waste in the river. There were many issues.”
All that has changed and as a group of senior Hayleys’ executives, PR agency staff and a Business Times team one morning last week drove into the facility, the visible quiet complex, machines working, the Kalu Ganga (river)

Water fountain
flowing and a water fountain spouting clean water just near the gate, belied the challenges the management faced to re-establish this fabric plant as a major supplier to Sri Lanka’s main clothing firms including MAS and Brandix.
Losses
From a loss of US$3.5 million in 2012-13 and $1.3 million in 2013/14, the company has recovered to its first year of profits in 2014/15. Machines are humming, the gardens are green, waste water is treated through a new treatment plant and safe water flows into the river.
While the initial purpose of the visit by the Business Times was to check out the company’s new Innovation Centre, what impressed us most was the positive links with the village, an example of how ‘alien’ factories must learn to live with the environment, rather than control the environment (village and other resources).
“My first priorities were to get the village on our side, efficiently manage the workforce and tackle the financial health of the firms (marketing and customers). We were producing the best fabric,” noted Mr. Goonetilleke, explaining the sequence of events in a comfortable board room at the factory. A cup of tea with some old-time jujubes (soft candy) helped us through the conversation.
“When I (first) came in I met one of the priests and also visited other temples. Through Buddhist monks in the six temples we were trying to reach out to the ‘opinion makers’ and convince them that the facility is an asset to the village economy and not detrimental,” he said.
He continues to visit the temples once a month while the company provides a free meal to the village on the birthday of a monk. It took four to five months to build a rapport with the village.
“We spent millions on a new water treatment plant and build a pond and a fountain which is on the road to the factory for people to see the clean water that goes into the river after purification,” he said, adding that it was all about building trust and faith with the village.
The factory uses four million litres a day which is treated after use and sent back to the river. The waste is sent to Holcim’s Geocycle plant.
“Temple priests in their sermons began speaking about the positive aspects now compared to before. People began to believe that we were not an evil force; rather wanting to do good (things),” he said. Every morning, at around 6.50 am, the Managing Director, who travels to the facility from his residence at Nawala, takes a walk across the factory floor greeting workers with a ‘good morning’ nod.
He uses an open, transparent management system to reach out to workers. “I tell them the reason for my overseas business trips; we discuss orders, performance and the balance sheet”.
Workers told company constantly losing money
Another lesson: Workers complained to the management that they were constantly told that the company was losing money. “We told them (company) that while we (workers) are working and working they (company) repeatedly says they are losing money. It was all negative vibes,” he quoted workers as saying.
A new culture was created, the workers were rejuvenated. The facility now produces 800 tonnes a month compared to 350 tonnes earlier with almost the same 1,180 workers. Incentives are provided and workers can get an extra Rs. 7000-8000 extra per month. Some managers also come and work on weekends voluntarily. Everyone is seen putting in their best effort.
With some 80 per cent of the workforce coming from the village, the links with the factory has strengthened over the past two years. The company helps village societies, provides support in flood relief. Last year when wells were flooded, the company disatched a pump and cleared 100 wells. Recently when a young mother jumped with her two daughters into the river, committing suicide, the company stepped in to help other members of the family.
Trying to get loans to rebuild the crisis-hit factory was another challenge. Banks had stopped lending due to continued losses. Armed with a loan from Hayleys, the Managing Director met the banks and explained the new, turnaround strategy. After months of reduced losses, the banks returned.
Just as the cup of tea is over and the delicious jujubes bowl on the board room table emptied by us (desperate to ask for a refill but too embarrassed to do so) -, it was time to visit the sprawling factory complex. Accompanied by Ajith Senaratne, Deputy General Manager – Quality and Development and Thushara Wijekoon, Product Design Engineer – Innovation, Mr. Goonetilleke, who is also a member of the Hayleys Group’s General Management Committee, took us across the entire floor area.
Massive bales of cotton and other yarn can be seen knitted together by giant machines. More investments, we are told, would be going into infrastructure to make the factory more efficient and the yarn better. The facility has a capacity of 1000 tons/month to knit, dye and finish all types of knitted fabrics such as cottons, cotton blends, polyester, polyester blends, viscose and micro modals. It also has the capability of in-house printing with 16 colour printing machines, fabric brushing machines and sueding machines.
Yarn from India
Yarn is imported mostly from India. Mr. Senaratne, one of the old management hands at the factory, explained that the dye and chemicals used are certified by international recognised certification companies ensuring the fabric is safe from skin and other allergies.
Walking through the wide, expansive factory, one of the machines is an attention-seeking one. Lovely prints are rolled out by the giant rollers ready to dispatch to the customer. At the back of the factory are several large ponds with different colours reflecting the water treatment process which then finally leads to the fountain which spouts, clean transparent water.
Newest attraction – the Innovation centre Ten years ago international brands would ask fabric makers to provide their suppliers tailor-made to their needs. That’s changing, rapidly. Now brands want fabric producers to come up innovative products and that’s what led to Hayleys MGT Knitting Mills to launch its own brand of fabric known as “Inno” which is developed at its own Innovation Centre. ![]() Water-resistant fabric. Created in January 2014, ‘Inno’ has already attracted key buyers to develop fabric for future seasons. They have also successfully managed to secure brand owner designers to select ‘Inno’ fabrics, the company says. As we walk into the cool, air conditioned Innovation Centre on the factory floor, a row of samples of different colours, designs and material catches our eye. Staff at the centre sits behind computers developing new designs. Mr. Wijekoon, the Product Design Engineer, explains the concept and shows some unique fabrics that they have developed. At one point, he picks out an orange cloth sample – off a sample book – and with a pipette gently drops small blobs of water on the cloth. It stays that way and doesn’t dissolve. “This material has been developed to be water resistant outside and absorbent inside,” says Mr. Weerakoon peering at the cloth. He then asks me to smell a white cloth sample which gives off a minty smell. Rubbing it vigorously, I am told to smell it again – this time giving a much stronger and pleasant mint smell. “The smell will remain for many washes in this particular fabric,” Mr. Weerakoon said, proudly as the rest of the team looks on with happy faces. |