Making waves by transforming plastic garbage into productive use
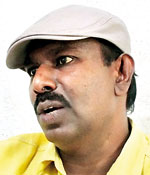
Damith Nishantha
HORANA – While Sri Lanka still appears to be struggling with garbage, waste polythene and plastics, there is a silver lining in the case of polythene and plastic waste. Recycling is fast becoming a cottage industry with a few large polythene recycling plants.
A true lover of nature, Damith Nishantha of Wagawatte junction, Poruwadanda, Horana at ‘Senasuma Polythene Recycling Centre’, has strived hard to keep the environment clean.
He first got involved in garbage recycling in 2002 and then changed to polythene waste recycling in 2005, a venture which was supported by the National Science Foundation (NSF). To witness this recycling plant in this remote village in Poruwadanda, the Business Times (BT) was accompanied by Suchima Gonapinuwala, Scientific Officer, NSF.
In 2002 Mr. Nishantha started a massive municipal and community garbage recycling project of the Horana Pradeshiya Sabha (now Urban Council), Bandaragama PS, Bulathsinhala PS, Seethawaka PS and Maharagama Urban Council and per day was handling 80 tons of garbage for recycling to ‘compost’. A slight hick-up in 2005 made him to divert his venture to recycle waste polythene. His service towards protecting the environment won him a Presidential Award of Excellence in 2004.
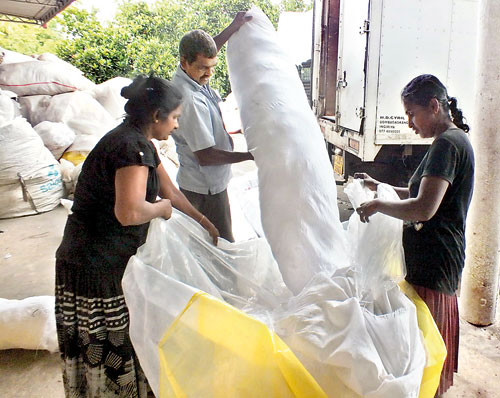
Unloading waste polythene from the lorry.
At the village, he said that when he started his venture he did not have any capital but only Rs. 175 and today has so far invested nearly Rs. 85 million.
He did bio-science for his Advanced Level and then followed courses in Business Management and Computer Science at NIBM, but nothing that was mechanical or technological. Yet, all the sophisticated machinery for the recycling garbage and polythene has been turned out by him.
He first turned out a compactor and a pelletizer, then later a crusher with improved technology, while the dirty polythene was washed manually. Ms. Gonapinuwala of the NSF told the BT that though there is the recycling plant, a major problem was the moisture retention in half dried waste polythene and had to be dried twice with a dryer with enormous power consumption at high cost. Mr. Nishantha then applied for a grant to turn out a machine to dry using minimal power at low cost. The blueprint was approved and a grant of about Rs. 5 million was awarded under the Technology Development Grant Scheme of NSF.
Mr. Nishantha has now introduced a polythene filming machine, a bag making machine and a printer to print on the bags. Now orders are entertained to make printed bags – the whole process is complete with his finished products in the market. He said that he now produces more than 5,000 kg per day.
Dr. (Ms.) Thamara F. Dias, Director General, NSF told the BT, the moisture retention in half dried waste polythene was the major problem where proper pellets couldn’t be made. She said that this entrepreneur took the initiative to manufacture the machine locally at a very low cost compared to an imported one.
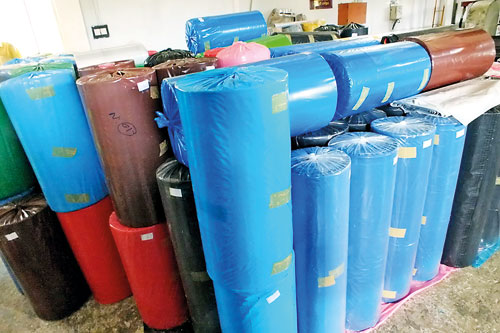
Finished and packed polythene films for bag making.
The machine, Dr. Dias said, is capable of producing 400 – 600 kg of pellets per hour resulting in a pellet kg at Rs. 160 compared to Rs. 280 made from imported recycled pellets. She pointed out that as such considerable amount of recycled polythene pellet imports can be reduced by adapting and using this technology. Mr. Nishantha said that there is also non-recyclable waste polythene but now he has created a process to recycle them and make environmentally friendly boards. These non-recyclable polythene includes BOPP (Bio Auxiliary  Polypropylene) and illuminating PET (Polyethylene Terephthalate). Direct orders are accepted and there are also two centres to sell his products. He employs 42 at present.
He says the waste polythene of the entire country could be handled, if a proper supply chain could be maintained. He indicated that there are 756 Grama Niladhari divisions in the Kalutara district and with the help of community service organisations they are planning make a central unit with the help of the Central Environmental Authority (CEA) and others and initiate a mass collection process to recycle the entire waste polythene in the Kalutara district.