News
Building industry booming, but not so workers’ safety
Outdated legislation, shortage of qualified inspection officers and a lethargic attitude towards occupational health and safety are among the major obstacles in averting accidents at construction sites.
Safety issues in the construction sector have come in for particular focus as it is one of the fastest growing industries in the country and also employs a large number of workers. It is also one of the most hazardous industries, with workers employed in often difficult and dangerous environments. While accidents are a major threat, diseases such as dengue too have become a health hazard at construction sites as there are plenty of areas where water can collect.
Occupational health and safety in the country is governed by the Factories Ordinance Act No.45 of 1942 which was promulgated from January 1, 1950. The ordinance, which has been amended from time to time, also covers the construction industry. Nevertheless, key regulations governing occupational safety and health have still not come into force, officials acknowledged.
The Factories Ordinance has 131 chapters and makes provisions for the safety, health and welfare of workers in ‘factories.’ Yet, the definition of what constitutes a ‘factory’ under the ordinance is outdated and as such, does not cover all workplaces. Authorities hope to address shortcomings in the Factories Ordinance through the proposed Occupational Safety, Health and Welfare Act, which would change the definition of ‘factory’ to that of a ‘workplace.’ This legislation however, has been pending for more than 10 years and is yet to be finalised.
A 2016 study by the World Health Organization (WHO) Collaborating Centre for Training and Research in Occupational Health on occupational health and safety in Sri Lanka, notes that even the enforcement of existing legislation has not been satisfactory due to various constraints. It notes that many small and medium sized industries do not pay due attention to occupational safety.
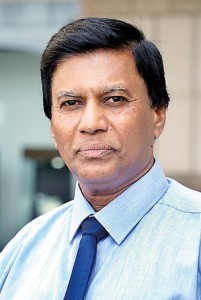
Lakshman Jansz
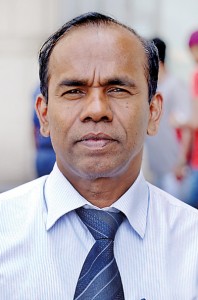
E.Abeysiriwardena
There is a clear inter-relationship between work and health, noted Dr Champika Amarasinghe, Director of the National Institute of Occupational Safety and Health (NIOSH). “If the worker is healthy, the work can be performed 100% effectively and productively. If the workplace is not healthy, workers will be affected. They may get sick or fall prey to accidents. The fact is that all occupational diseases and accidents can be prevented,” she emphasised.
The NIOSH is a policy-making body under the Department of Labour and its mandate is to create awareness, conduct training and carry out research on occupational health and safety. One of the main challenges is that the subject is not being taken as a serious issue across the board in almost all industries, Dr Amarasinghe observed.
Enforcement of the Factories Ordinance is vested with officers of the Industrial Safety Division (ISD) of the Department of Labour. Nearly 30,000 have registered so far, but the division estimates that a far bigger numberfalls under the current ‘factories’ definition.
The ISD, however, is struggling to do regular inspections of even the registered places due to a lack of qualified factory inspection engineers. The position requires highly qualified individuals with a minimum qualification of a Bachelor’s Degree in Engineering. Currently, only about 25 such engineers work at the division, spread across 10 District Engineers offices island-wide. The approved cadre for factory inspecting engineers is still only 37, but given that the number of registrations are increasing every year, officials said they would need around 100 engineers to do a thorough job.
Despite the shortage of personnel, the ISD carries out its work to the best of its ability. The division files legal action regarding serious violations of occupational health and safety. Nearly 30 such cases against various companies are currently before courts. The cases have been filed over failure to report accidents and failure to ensure a safe place of employment for workers, said Lakshman Jansz, Commissioner of Labour (Industrial Safety) & Chief Factory Inspecting Engineer/ Add. Commissioner General of Labour- Enginering (Act.).
Encouragingly though, there is an increase in accident reporting due to awareness campaigns at construction sites, he revealed.
Major contractors are also taking measures to follow industry ‘best practices’ by adhering to the Factories Ordinance and even going beyond it on occasion to prevent accidents at construction sites, officials stressed. These include making Personal Protection Equipment (PPE) mandatory for all employees, clearly designating and displaying emergency assembly points, as well as instaling handrails, safety netting and other barriers to prevent falling hazards.
Yet, in general terms, there is still a lackluster attitude towards safety that needs to change urgently, said E. Abeysiriwardena, Specialist Factory Inspection Engineer at the ISD. He observed that many workers at construction sites in urban centers are from rural areas. A considerable number have only worked in single storey buildings. No matter how hard companies try, it is difficult to convince these persons, who have got used to working without any safety equipment, to wear them continuously while working, he lamented. “They think an accident will not happen to them. They keep on thinking that until it does.”
Some contractors too are guilty of compromising on safety by cutting down the amount of funds they spend on safety measures. They fail to realize that ensuring a safe working environment for workers benefits the contractor in turn, Mr. Abeysiriwardena said, adding, “We need a complete change of attitude towards safety among workers and employers. The focus should be on preventing workplace accidents.”
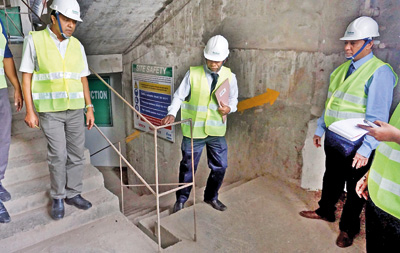
Some of the safety measures that should be adhered to at construction sites. Pix by Ishanka Sunimal
Those in the industry too believe that an attitude change is needed. Athula Galagoda, Chairman of the National Construction Association of Sri Lanka, stated that younger workers were more receptive to wearing Personal Protection Equipment (PPE). The older ones aew more difficult to persuade. “They have been working in the industry for years without them and so balk at the idea of being forced to wear such gear,” he remarked.
He urged authorities to reduce the customs duties on PPEs and hi-tech tools that come with enhanced safety measures, pointing out that if the items were cheaper, it would encourage contractors to invest in them.
Mr Galagoda though, said, efforts to minimise construction industry accidents will only be fully successful if occupational health and safety measures are made compulsory for all by law.