DC coconut industry: Making it energy efficient
The major energy sources used in Sri Lanka are biomass and oil. In 1999, biomass (mostly firewood) accounted for about 51 per cent of the national primary energy consumption, of which about 24 per cent was consumed in industries, such as the tea, desiccated coconut (DC) and rubber industries. Fossil fuel (oil and a small quantity of coal) accounts for about 37 per cent of the total energy consumption, which is totally imported. Between 1999 and 2000, the country’s oil demand increased by 14 per cent. Hydropower accounted for 46 per cent of the installed capacity, and the rest is from fossil fuel-based thermal power plants.
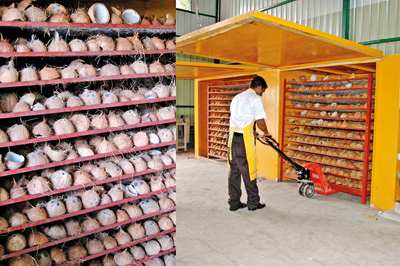
File picture of a coconut products factory.
Coconut has been the third most important commercial crop of Sri Lanka since the colonial era. Sri Lanka is the world’s fourth largest producer of coconut.
DC is a dried white, shredded product manufactured from the peeled kernel of seasoned coconut under hygienic processing conditions. It is used in the bakery and confectionery industry for fillings for nut bars, cookies, biscuits, sanding of cakes, pies etc. It is estimated that to produce 1 ton of DC, 8000 nuts are required. Sri Lanka is the world’s second largest DC producer sharing about 25 per cent of the global annual DC production.
It is the highest foreign exchange earner in the Sri Lankan coconut processing industry.
Cost of the raw material, coconut, is responsible for a major portion of the total cost (90 per cent). For its survival and growth, the DC industry has to implement cost cutting measures by improved process efficiencies, such as energy conservation and management, and adopting cleaner production technologies.
Production process
The level of technology employed by the industry is not sophisticated though maintaining hygienic conditions is of paramount importance, as the product is a food item.
The drying equipment is considered as the heart of the production process. They operate at around 42 per cent efficiency and are generally fueled by firewood/liquid fuel through air heaters. Modernised mills are considered to be superior in terms of product quality and hygienic conditions of the factory environment.
There are a series of operations in the DC manufacturing process, viz. hatcheting, paring, pairing, sterilising, cutting, drying, grading and packing. The drying process, which is the most energy intensive, reduces the moisture content from around 52–55 per cent to 3 per cent.
Energy usage of DC industry
Heat and electricity are the two main energy forms used in DC mills. Thermal energy is used to produce hot water, steam for pasteurisation/sterilisation and hot air for drying. Electrical energy is used for driving conveyors, motors, blowers, mechanical de-shellers, sifters and screening, grading and packaging machines.
Electrical energy
The average specific electricity consumption varies between 0.10 and 0.13 kW h/kg of DC and the electrical energy consumption in modern mills is higher compared to traditional mills due to the use of more electrically operated machineries. In terms of unit operations, drying consumes around 60 per cent of the electricity, the highest amount among the unit processes. The size reduction and screening processes account for 30 per cent and 10 per cent. The electricity demand of modernised DC factories varies from 75 to 115 kVA, while in conventional or traditional factories, it averages around 37 kVA.
Thermal energy
Thermal energy constitutes about 90–95 per cent of the total energy consumption, and about 85 per cent of the total thermal energy is consumed in drying with the rest in pasteurising or sterilising. The specific thermal energy consumption of modernized DC factories varies from 2.13 to 2.65 kW h/kg of DC, while in traditional factories, it averages around 6.46 kW h/kg of DC.
The high thermal energy consumption in traditional mills is due to the inefficiencies and large losses in the desiccators. Old tray type desiccators consume about 1.5–2 times more energy than advanced continuous dryers and take a longer drying time (nearly 45 mins compared to 15 mins for advanced dryers). Hot water pasteurisation consumes about 2–2.5 times more energy compared with steam sterilisation. Losses in the blancher are also due to the loss of hot water during loading and unloading of meats from the blancher and surface (convection and radiation) losses.
Incomplete combustion of firewood and low efficiency of burners in wood fired boilers (about 10–15 per cent lower than oil fired boilers) also reduce the overall efficiency of the system.
Pollution aspects
Two types of waste, liquid and solid, are generated, apart from the gases produced during the combustion process of fuel. The main waste is the coconut water (sap), which is mixed with normal washing water and discharged, with a little treatment, to neighbouring lands and water bodies, causing severe environmental damage to vegetation, ground water resources and water bodies. The only treatment done is the removal of oil sludge after allowing the wastewater to be retained in open pits for some time. This sludge is sold as a lubricant to the tile industry. In traditional mills, where firewood is used to generate hot air, wood ash is a waste product. These ash stocks are dumped on the factory premises itself.
Though the coconut shell is a waste in the process of DC manufacturing, it is either sold to charcoal manufacturers or burned within the premises to make charcoal. Likewise, coconut scrapes (parings) coming out as a waste during the scraping process are sold for extraction of coconut oil.
Local pollution
The industry is saddled with a local environmental problem due to the large quantities of wastewater that have to be discharged. Wastewater has high concentrations of biodegradable compounds, including carbohydrates, oil and grease. A typical factory with a daily capacity of 50,000 nuts, discharges around 40,000–60,000 l of wastewater. This results in a total discharge of around 620,000 tons per annum and the industry enjoys the freedom to discharge wastewater without being resisted either by neighbours or by environmental authorities.
GHG and other emissions
The gaseous emissions of the Sri Lankan DC industry due to the combustion of fuel oil (in modernised factories) and firewood (in conventional factories) has been estimated as:
- CO2 72,500 tons per year CO 7000 tons per year
- SO2 250 tons per year NO2 30 tons per year
- The total CO2 emission of the industry accounts for about 1 per cent of the national figures
- Improving energy efficiency /environmental friendliness
Though the industry is economically important, it has to struggle for its survival due to supply and demand constraints, process deficiencies and inefficiencies arising from technology obsolescence, escalating input costs and, more importantly, the environmental challenges. Some of them indeed are beyond the control of the industry. Some options available to the industry are described below:
Energy efficiency can be improved by adopting better operational and housekeeping practices and using energy efficient boilers and desiccators.
(a) Better operation and maintenance of existing equipment, such as improvement in the performance of tray type desiccators by reducing their idling time and synchronising the upstream production with the drying cycle, would improve their efficiency,
(b) operating at rated capacity and controlling the quantity and temperature of the supplied air and residence time can reduce energy use, and
(c) insulation of desiccators and reduction in loading/unloading time of coconut meat can help achieve further energy savings.
Boiler performance
This can be improved by operating at the correct air–fuel ratio, preheating combustion air, regular cleaning of burners etc. The efficiency of heat exchangers can be improved by insulation, removing scales and repairing leaks in the heat exchanger coils. Condensate loss and pipeline losses can be reduced by regular maintenance of transmission lines and insulations. For example, the condensate loss of about 40–60 per cent can be recovered by operating in a closed loop system. This would reduce the condensate heat loss to about half and also promote water recycling.
Waste heat recovery can be another important means to reuse heat, and it is estimated that about 20 per cent reduction in fuel consumption is possible by installation of suitable waste heat recovery systems.
Other technological options Efficient dryers
The dryer is the most critical and highest energy consuming unit in a DC factory and is responsible for the consumption of around 90 per cent of the total thermal energy. Therefore, any improvement in the dryer will have a significant impact on the cost of production.
Coconut shells as a source of energy
It is estimated that a very large quantity of coconut shell per year is made available as a byproduct of the DC industry. Over 90 per cent of this is burned in open pits to produce charcoal for the activated carbon industry. This process emits a lot of harmful gases, creating severe environmental problems. If efficient carbonisation of coconut shells was adopted, the waste heat of the process could be used for generating steam, and the environmental hazard could be eliminated.
Wastewater treatment
It is expected that the BOD and COD levels of the wastewater after treatment will be reduced to acceptable limits, and the biogas generated (1 m3 of biogas per 2 m3 of wastewater) will find useful applications (to supplement boiler fuel, lighting, water boiling in the canteen and in the laboratory etc.) within the factory.
Technical/ Energy Audit
An energy audit is an analysis of a facility, indicating how and where that facility can reduce energy consumption and save energy costs. Its insight to energy efficiency and conservation can lead to significant savings on the company’s utility bill.
It’s important to take advantage of any tips, programmes and incentives that will conserve energy. There are measures that will generate savings to positively impact your bottom line immediately, as well as longer-term strategic initiatives to assess your needs and stabilise your energy spend in the longer term – which is great news for your budget!
Conclusion
Beyond doubt, the DC industry is one of the nationally important indigenous industries of Sri Lanka. Therefore, it is the responsibility of all stakeholders to contribute to the sustainability of the industry. Though DC production is not very energy intensive, the energy use influences the overall efficiency of the DC mills operation and the cost of production. For the Sri Lankan DC sector to be competitive in the global market, measures to reduce energy consumption would help to reduce the cost of production and generation of pollutants.