Lankan rail bridges can still be saved
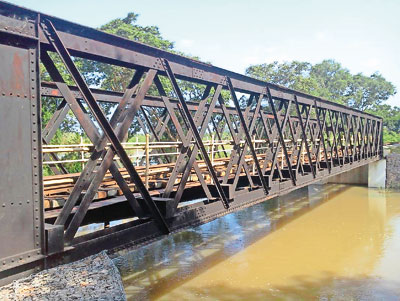
Figure 1: Truss Bridge showing various elements
Some time ago, rail bridges in the Puttalam area were inspected as part of a study to evaluate their condition. “Instead of building a brand-new bridge, we proposed to repair the existing rail bridge by retrofitting the worn-out parts,” said Professor Ranjith Dissanayake from the Department of Civil Engineering of the University of Peradeniya. As a result, the financial saving was in excess of Rs. 30 million. Meanwhile, a research proposal to the National Research Council (NRC) was accepted for funding, leading to many important findings on the feasibility of reinstating specific elements of a bridge rather than replacing it entirely.
The problem: The old rail bridges
Many of the bridges in Sri Lanka were built over a 100 years ago when the railway system was constructed. At that time, most of the bridges were made of iron. Many of these have endured while providing services transporting people and goods over the years. A typical example is the railway bridge at Peradeniya by the Colombo-Kandy main road. In Sri Lanka, old iron bridges on railway lines have survived in spite of challenges in maintenance.
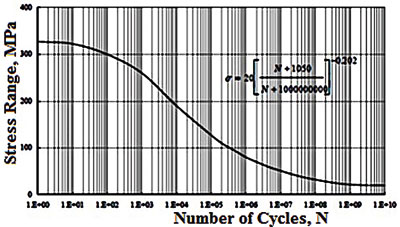
Figure 2: Wohler curve for wrought iron (fatigue strength)
Building a new rail bridge involving the dismantling of the old bridge and constructing a new one is costly. Many low-income countries face the same problem. When constructing a new bridge, the number of vehicles, the type of load (inclusive of unavoidable loads such as floods and wind), and the fatigue in the metal have to be considered, thus increasing construction cost. On the other hand, if an old bridge is unusable or fails under load, the damage caused to people and the economy will be enormous, quite apart from the inconvenience to its users of not having the bridge. The obvious compromise is of course the rehabilitation of existing bridges.
A solution: Rehabilitation of the existing bridge
Rehabilitation of a bridge requires the study of the structure and analysis of its parts for their strength and deficiencies. In that way, the remaining age (or the life time of the bridge) is estimated. Knowing which parts are weaker than others enables their replacement so that the entire bridge would live out its design life.
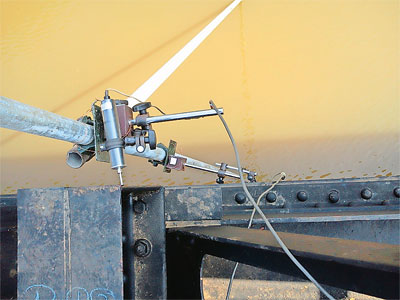
Figure 3: Electronic in-situ measurements
A rail bridge considered in this study was the 165m-long Kelaniya Railway Bridge, which is a nearly 150 -year-old truss bridge made of wrought iron (rather than steel that is used today). Fig. 1 shows a typical truss bridge form with its many parts or elements. Initially, the length, the width and the thickness of all the elements of the bridge were measured. Information regarding tears in the iron and weak points was obtained from X-ray analysis. For material testing, the steel samples taken from the bridge were tested in the laboratory by chemical analysis, microscopic examination and mechanical property tests to identify the type of iron, its elastic modulus and types of strength (e.g. yield, ultimate and fatigue). It is yield or ultimate strength that is used as the basis of design under normal circumstances, but the fatigue strength under repeated load cycles can be an order of magnitude lower – see Fig. 2, which indicates that the allowable stress range will be drastically reduced with an increasing number of stress cycles (e.g. due to loading and unloading).
The next step is to perform the field load test. When trains travel on the track, various parts of the bridge experience extensions, contractions and vibrations depending on the load carried. These are measured using electronic transducers, strain gauges, acceleration gauges and electronic data loggers (Fig.3). Thereafter, a virtual computer model of the actual bridge is developed and validated. Computer-simulation technology is used to construct a virtual bridge which is compared with the actual bridge in question. To build a virtual bridge, the dimensions of the bridge and its current condition are treated as inputs. The virtual bridge can be validated by imposing loads on both the real and virtual bridges, measuring deflections and strains in the real bridge, and checking whether the virtual bridge outputs are similar to measured values. After validation, the performance of the real bridge under even say earthquake forces can be estimated by imposing such forces on the validated virtual one.
The train time tables would indicate the number and magnitude of repetitive forces that need to be imposed on the virtual bridge for a target duration of bridge life. The stress ranges and the number of cycles experienced can be calculated. The fatigue strength drops significantly with the number of cycles (Fig. 2), and hence has to be estimated carefully.
Using the virtual bridge, the remaining bridge life is calculated, assuming that railway time tables and rolling stock loads will not change significantly. Even if they do, the virtual bridge can once again be used for simulation. This remaining bridge life can be calculated for the different elements of the bridge. If a particular part has very low remaining life (or in fact its life is theoretically exceeded), that part can be replaced via retrofitting. Thus, instead of building new bridges, the existing bridges can have their suitability checked and retrofitted accordingly.
The benefits and
conditions
A considerable economic benefit through selective retrofitting (rather than replacing the entire bridge) is the main advantage. This type of targeted reinstatement of elements would probably incur only 5-10% of the cost to replace the entire bridge. Such retrofitting is also much faster than the time taken for new bridge construction. Rehabilitation reduces the need for new material, thus reducing carbon budgets and other adverse environmental effects too. In order to reap these benefits safely however, regular maintenance and periodic retrofitting of the rehabilitated bridge would need to be carried out.
If such maintenance is undertaken, the method developed in this research for evaluating the remaining age of existing rail bridges in Sri Lanka would both save money and protect the environment.
This work was carried out by Eng. Dr A.M.A.C.S. Bandara (csbandara@eng.pdn.ac.lk) and Eng. Prof. P.B.R. Dissanayake (ranjith@eng.pdn.ac.lk) at the University of Peradeniya, from whom more information can be obtained. Professor Dissanayake is the current Chairman of the Green Building Council of Sri Lanka and was recently appointed as the Secretary of the State Ministry of Rural Roads and other Infrastructures. The research was funded by the National Research Council Grant IDG 11-106. Asitha Jayawardena was commissioned to write this article as part of the science publicity programme of the National Academy of Sciences of
Sri Lanka.