News
Builders being bulldosed by cement shortage, small contractors badly hit
Small building contractors are going bankrupt due to the shortage of cement and other construction materials and the increasing cost of items such as reinforcement bars.
The Chamber of Construction Industry Chief Nissanka Wijeratne said 80 percent of construction materials were imported, and builders were finding it difficult to acquire products at reasonable prices as the depreciation of the rupee and the foreign currency shortage had forced importers to raise prices.
Due to the shortage of foreign currency, importers were unable to open letters of credits and were buying foreign currency at black market prices, he said.
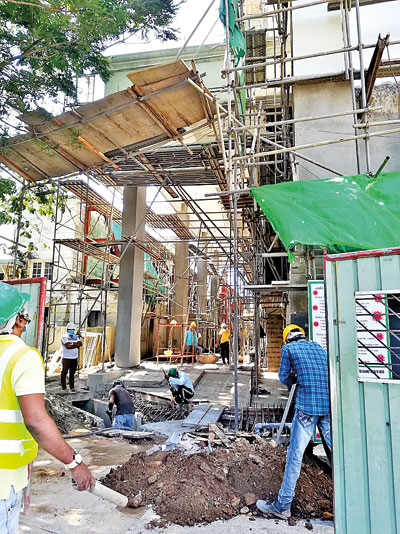
Shortage of cement was making it difficult to finish projects on time. Pic by Nilan Maligaspe
Lack of materials, high costs and delays in projects were driving small construction contractors bankrupt.
While the government was instigating more development projects, potentially increasing opportunities for building firms, most private and government projects were not factoring in price escalations, Mr. Wijeratne said.
He urged the government to make laws making it essential to provide a price fluctuation formula when material prices rise, and to release foreign currency to importers to allow them to bring in materials.
One building company owner, Asantha Jeewanaath Pinto, said the shortage of cement was making it difficult to finish projects on time.
“Our company is engaged in hotel, roads and bridge construction. When our projects are delayed the country’s development is delayed as well,” he pointed out.
Mr. Pinto said when projects were delayed constructors had to pay up to 10 per cent of the building cost to the client as liquidated damage.
He added that when materials such as cement were scarce, labourers and masons sat idle. Such interruptions in work schedules affected the quality of construction.
“There can be technical complications if we delay the addition of cement at the proper time,” Mr. Pinto explained.
Another construction company owner, Shantha Dickwella, said cement had no substitute, so shortages dictated prices.
“Apart from big companies, which are equipped to store cement, builders are unable to keep cement stashed for long periods,” he said.
Some hardware shops appear to be exploiting the situation. The Sunday Times observed that people buying cement were being informed that other purchases must also be made.
The Chairman of the Tokyo Cement Company (Lanka) PLC, Dr. Harsha Cabral, said his firm was ramping up supply to meet demand but was hampered by an unavailability of bulk cargo carriers.
Mr. Cabral added that there were delays in opening letters of credit with banks, “where the process that happened on the same day now takes weeks”.
A leading official of the Construction Industry Development Authority, Savindra Amarasekara, primarily blamed a price-controlling mafia for price increases although he acknowledged that the dollar shortage and depreciation of the rupee were contributing factors. He said whenever the government imposed price controls the mafia staged protests or created artificial shortages to get their way.
Mr. Amarasekera, who is the authority’s Director of Development, said 70 per cent of the six to seven million metric tons of cement used annually was imported.
Even though most cement packaging claimed the product was locally made, the bags included imported cement, and merchants increased prices across the board, including on the local product, he said.
The State Minister of Co-operative Services, Marketing Development and Consumer Protection, Lasantha Alagiyawanna, said cement importers had brought to him their concerns about a difficulty in arranging freight carriers during the pandemic.
As well, importers had pointed out that even though the imported cement is quality-approved by the Sri Lanka Standards Institute there was a problem with locally-printed packaging.
“Therefore, as the state Minister in charge I instructed the institute and the Consumer Affairs Authority to resolve the approval issue for the packaging and urged importers to bring in more imports so the shortage would decrease in two weeks,” he said.