US
funded FIPs upping garment factory productivity
By Dilshani Samaraweera
A US funded factory improvement programme
is boosting productivity in garment factories. The Employers
Federation of Ceylon (EFC), the implementation agency
of the factory improvement programme says factories
that participated in the training are showing noticeable
improvements.
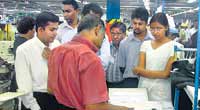 |
A training session in progress |
“There is an improvement in quality
through the reduction of defects, both in-line and end-line.
There is an increase in productivity, for instance increased
cutting department efficiency and sewing to packing
efficiencies. There is reduction in labour turnover,
absenteeism and sample turnaround time,” said
Jayantha R de Silva, regional specialist, International
Labour Organisation (ILO)/ EFC Factory Improvement Programme
(FIP).
Sri Lanka’s garment factories
are under increasing pressure to produce better quality
at lower prices after world garment quotas ended in
December 2004. To stay in business and compete against
lower cost but more productive countries like China,
Sri Lankan garment factories are now forced to take
a second look at their operations.
The FIP is a project under the ILO’s
Management and Corporate Citizenship Programme and the
EFC is the local implementing agency. The programme
is funded by the US Department of Labour with contributions
from participating factories and is implemented in six
developing countries including Sri Lanka. In Asia, countries
like Vietnam and India are recipients of FIP funding.
The US funding comes to over US$ 1 million for the six
country programme over a period of five years. The project
has wide support from multinational corporations that
are also big buyers of US clothing brands from Sri Lankan
garment factories.
“The first FIP in Sri Lanka
was in 2002. We have now just launched the fourth FIP.
In Sri Lanka we have standardised the programme to a
one year programme with six modules and a section on
labour laws,” said de Silva.
However, the programme has so far
only been able to accommodate 27 out of over 700 Sri
Lankan garment factories. The most recent headcount
of garment factories conducted in 2004 by the Labour
Department and a coalition of trade unions and NGOs,
found 733 garment factories in the island compared to
a previous 830.
Training tells
The FIP training says the EFC has shown companies how
to increase output with available resources. The results
of the latest FIP shows that companies have managed
to cut down on the time taken to meet a sample order.
“The sample turnaround time of the participating
companies reduced, on average, by 28 percent,”
said de Silva. Meanwhile needle down time, or the physical
sewing time, increased by six percent. Sri Lankan garment
workers are generally considered lower in productivity
than, for instance, Chinese workers due to the much
lower productivity indicators like the needle down time.
“When a worker sits at a sewing
machine only a certain part of that time is spent on
actually sewing. The needle down time in Sri Lanka is
around six to eight percent compared to over 20 percent
in China. This is because in China the workers are paid
on a piece rate. Workers are paid on how many items
they produce and as a result they spend more time on
actual production. However, after the FIPs, on the whole,
we were able to increase needle down time on average
by six percent among participating companies,”
said de Silva.
The FIP, says the EFC, has helped
factories cut down on costly rejects. In-line defects
reduced from 43 percent – 8 percent and end line
defected dropped from 40% - 15% during the first and
second round of FIP training in some factories. The
third FIP saw a 9 percent drop on average, in in-line
defects.
Garment factories are also learning
to use productivity-aids to increase their efficiency.
For instance, the attachment usage rate increased by
57 percent after the programme. Attachments are tools
that are specially devised to speed up output.
Improved efficiencies lead to cost
savings. The operating cost per minute, says the EFC,
was reduced by 23 percent. “In China the cost
per minute is around US$ 0.3 to US$ 0.4 per minute.
In Sri Lanka it is generally over US$ 0.5 per minute
and going into double digits, which can be disastrous
for factories. These higher costs are due to various
factors but what it means is that we work longer but
produce less,” said de Silva.
Labour turnover per month reduced
by 12 percent on average and the programme helped improve
management-worker relations as well, says the EFC. “The
management has understood that workers not only work
but can think and work and also have ideas to contribute,”
said De Silva. Factories were also persuaded to invest
in better training and to encourage multi-skilling.
The EFC says it is currently in the
process of signing up factories for its fourth round
of FIPs. “We can only accommodate a limited number.
Up to 12 factories have the opportunity to participate,”
said De Silva.
|