At the Wijeya Newspapers offices on Hunupitiya Cross Road, Colombo 2, the heavy rumbling of the presses on the ground floor is a familiar sound. But the Sunday Times is not printed in one place or even at one time – instead the paper gets neatly divided into sections. A heavy printing schedule for the Sunday paper begins mid-week and ends only in the wee hours of Sunday morning itself, as crisp editions of the paper slide off the presses.
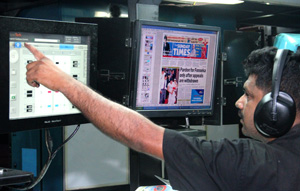 |
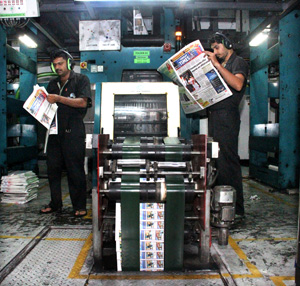 |
Focus on quality: The printing dept. staff at work. Pix by Indika Handuwala and Nilan Maligaspe |
At their peak performance, these machines can turn out up to 45,000 copies of a 28-page newspaper in an hour and their ability to print high quality images in rich, clear colours is highly valued. The advantage lies in their superior ink balancing and registration. The latter refers to the process by which a machine blends the basic colours of cyan, magenta, black and yellow to bring you the full colour palette, explains Assistant General Manager Production, Rohan David, who is on the team at the Wijeya offices in the city.
He has been with the company since the Sunday Times was launched 25 years ago, and says he’s seen the printing become increasingly computerised.
Their presses are run with a relatively small staff of 65, says Assistant General Manager - Press and Production, Dhammika Wimalarathne. These machines are experienced workhorses, each having served the company for more than a decade. However, when the need was felt to expand and improve the printing, the company knew it would have to find space outside the city. That was when the Hokandara complex was built and it is where most of the paper is currently printed.Installed on the premises is a hi-speed auto registration four-colour web offset (Hi-Line) printing machine that uses CTP technology with environment-friendly chemicals. The use of the automated off-line inserting machine (KANSA) is believed to be the first such installation for the entire South Asian region.
The state-of-the art facility has won a host of awards recognising its green initiative and clean production standards. Since the complex was opened in 2008 it has collected several awards including the National Quality Circle Bronze Award in 2010 from the National Productivity Secretariat, as well as the 2010 Taiki Akimoto 5S Awards awarded from the Japan-Sri Lanka Technical and Cultural Association (JSTACA). Other awards include the the National Cleaner Production Awards in 2009 and 2010 and the 2010 Chemical Leasing Global Award from the United Nations Industrial Development Organization (UNIDO).
They are also undergoing the rigorous process of ISO 14000 environmental management certification but in the meantime, the company’s many eco-friendly projects are already established.
For instance, the water that is used in production is collected into a central tank, explains Janaka Rathnakumara, Assistant General Manager at the complex. Cleaned and recycled, it is reused for housekeeping and gardening on the grounds.
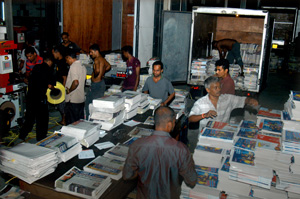 |
Speedy delivery: Despatch dept. staff playing a key role |
The complex was designed so that its interiors could be lit solely by natural light from 6 a.m. to 6 p.m. he adds, pointing out that this simple measure allows the company to shave an estimated Rs. 400,000 every month off its electricity bill. Waste management is taken seriously at the complex – from the way food and packaging is dealt with at the canteen to the lengths of waste paper left over from the printing. Separate bins for organic waste, plastics and recyclables direct each material down a separate path – whether it is toward the on-site compost heap or toward a recycling facility. Mr. Rathnakumara, who first joined the paper as a mechanical engineer and has climbed the ranks is proud of what they have accomplished – most companies try to go green because the buyers prefer that, he says adding, “we did it without any buyer requirement.”
|