Sandy treasures
of Pulmoddai
Titanium
- strategic metal of high value
Ilmenite is used to make titanium metal, a strategic metal
valued for its high strength and light-weight. Titanium is
as strong as steel, can withstand very high temperatures and
is non-corrosive. Its high strength-to-weight ratios make
titanium ideal for high-performance military aircraft and
rockets, space capsule skins, armour plate, aircraft firewalls,
jet engine components, landing gears, submarines, and engine
parts (as an alloy).
At one
point during the height of the Cold War in the mid-1980s,
Moscow stopped exports of titanium when large quantities of
the metal were required to build Alfa class attack submarine
hulls.
Titanium
is used to make paint, paper and plastic. Its properties ensure
that exposure to sunlight does not alter its very white colour.
It is also used in desalination plants.
"Titanium
is regarded as the metal of the future," said Nandadeva.
"The industrial world cannot do without it and there
is no substitute for it."
Rutile
is mainly used in the titanium metal industry and in welding
rods while zircon is in demand in the ceramic industry for
high quality glazing, foundries, and electrical items.
Rich deposit
The Pulmoddai deposit is four and a half miles long and 600
metres wide. Mining starts around February from the Arisimalai
end of the deposit on the southern side and ends in October
at the northern end towards Kokilai. The processing plants and
godowns along with the beach deposit covers 108 acres.
The beach
deposit is mined using an excavator dragline. Raw sand is
washed and screened to remove trash and shell fragments and
put through a series of concentrators to separate the heavy
minerals.
The usual
concentration of heavy minerals is 40 percent, said Nandadeva.
But if the deposit is left untouched for long periods it gets
upgraded or enriched to as much as 80 percent by fresh sand
brought ashore by the sea.
Mining
must be systematically done with a gradient left for fresh
sand to be deposited.
Raw sand
is first upgraded in a process known as gravity separation.
The ilmenite that is produced is processed further using a
magnetic separator and then put through a high tension separator
- where a current of 22,000 volts is sent through the sand
- to remove rutile. What remains is called crude zircon
The minerals
are taken from the godowns on a conveyor belt fixed onto the
800-foot jetty and then discharged into barges. The loaded
barges are towed by tugs to bulk carriers anchored offshore,
the draught at the jetty not being deep enough for the vessels
to come alongside. It takes several days to fill a bulk carrier
at the rate of about 2,000 tonnes every 24 hours. Repairs
to the conveyor belt and jetty are almost complete and the
plant is getting ready to resume bulk shipments before the
monsoon breaks.
The company
has three tugs and 10 barges, which it plans to repair as
they have been being laid up at Cod Bay, Trincomalee for several
years.
|
Kanijapura,
Pulmoddai - The godowns are full at the Lanka Mineral Sands Ltd
processing plant in this remote corner of north-eastern Sri Lanka.
The black sand that covers the beach - rich with heavy minerals
- has not been mined for almost five years - ever since Sea Tigers
sank a bulk carrier loaded with a cargo of ilmeniteabout a mile
offshore.
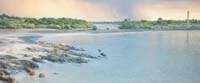
The Pulmoddai
beach deposit, where one can virtually walk on money, has two characteristics
that make it unique - the mineral sands get replenished with every
monsoon and the sand has a heavy mineral content that far exceed
that of deposits elsewhere in the world.
"Now that
the godowns are full we want to sell the accumulated stocks and
resume bulk shipments," S. A. Nandadeva, general manager of
the company told a team of Sunday Times Business journalists during
a recent visit.
A huge mound
of black ilmenite sand sits silently in one of the plant's cavernous
godowns, disturbed only by bats that have made it their home. Another
mound of white-coloured crude zircon lies in the open outside, being
dried with the use of a front-end loader.
Stocks consist
of 60,000 tonnes of ilmenite and 150,000 tonnes of crude zircon.
Another product - rutile - is being exported in 40-kg bags through
the Colombo port. About 5,000 tonnes have been shipped in this manner
and another 2,000 tonnes remain in stock.
North-east
monsoon
Pulmoddai does not have a sheltered anchorage and no shipments
are possible during the north-east monsoon, which usually blows
from October to March, when the seas can get very rough. No mining
is done either. It is during this period that sand washed ashore
by heavy waves renews the beach deposit.
"The conditions
here are right for the sand to be washed ashore," said Nandadeva.
"There is no erosion."
A little headland
separates the beach deposit from Arisimalai, which is also an interesting
little beach with white sand that looks like grains of rice. Nandadeva's
studies indicate that the tides and currents of the area and the
way they are shaped by the headland create the peculiar conditions
under which the sand that is mined is replenished in an annual cycle.
"The sand
containing heavy minerals gets concentrated owing to wave action,"
explained Nandadeva. "The light sand gets washed away leaving
the heavy minerals."
Beach deposits in Australia, a big producer of minerals, have concentrations
of only around five percent. The Pulmoddai site is rated as one
of the best in the world with a heavy mineral content of 60-70 percent,
making Lanka Mineral Sands one of the world's low cost mineral sand
producers. This means that up to 70 tonnes of heavy minerals can
be recovered from 100 tonnes of raw sand. "This mine is supposed
to be the richest in the world," said Nandadeva.
The main deposit
consists of around 60 percent ilmenite, eight percent rutile and
8-10 percent zircon.
Mahaweli
Surveys commissioned by the company indicate that the heavy
minerals actually come from the island's interior, being washed
down from the central massif by rivers such as the Mahaweli, as
well as the Yan Oya. Heavy minerals are released when igneous (volcanic)
rock gets eroded by rain and wind - a process that takes millions
of years. Recent studies have given rise to a belief that the volumes
of heavy minerals that get washed down from the central hills have
diminished with the damming of the Mahaweli.
The company
has mined only a limited area in Pulmoddai - the first deposit that
was surveyed in 1971 with the help of the Geological Survey Department.
This revealed a heavy mineral content of 3.7 million tonnes with
a cut off grade of 30 percent. At the present rate of mining, these
reserves are estimated to last for about 25-30 years. Other deposits
found in subsequent surveys between Mullaithivu and Nilaveli have
remained untouched. These are Kokilai and Nayaru, north of Pulmoddai,
and Paduvaikaddu and Thavikallu, south of the plant. Surveys, both
onshore and offshore, have estimated that there are more than 12
million tonnes of heavy minerals in Pulmoddai, Kokilai, Nayaru and
Mullaithivu.
The plant has
a capacity of 150,000 tonnes of ilmenite, 10,000 tonnes of rutile
and 6,000 tonnes of zircon. Annual production is 80,000 tonnes of
ilmenite, 7,000 tonnes of rutile, and 7,000 tonnes of zircon. Production
of zircon was stopped after the LTTE blasted the fresh water plant
at Yan Oya that supplied water to wash the minerals.
Royalty
The company pays royalty to the government for the mining rights
and was the most profitable among the companies under the Industries
Ministry at the time.
The main markets for the heavy minerals are in Japan and Europe.
The company usually sells to traders and is not aware of the ultimate
end-user of its minerals. Ilmenite is sold for around $70 a tonne
FOB, rutile for $400 a tonne FOB and zircon $500 a tonne FOB.
"There's
a lot of interest among foreign buyers and investors," Nandadeva
said. "We wanted to have a joint venture to make titanium dioxide
pigment or synthetic rutile (convert ilmenite to rutile grade which
fetches a higher price) and convert zircon to ceramic grade."
Five firms
showed interest but said they would come in only when there's a
durable peace. The joint venture plant was to have been between
Pulmoddai and Trincomalee from where shipments were to take place
throughout the year.
Workers at
the plant went through very tough and dangerous times during the
war, being virtually surrounded by LTTE-held territory. They could
not venture out of the premises at night, and even during the day
finding transport was difficult, said Wasantha Anurakumara, the
plant's administration officer. Power supplies were disrupted for
long periods, as were telephone services. An army unit was always
stationed at the site and came under repeated attack. The army dominated
the area during the day and the Tigers prowled at night.
The workforce
of 340 on the site is made up of all three communities and they
enjoy free housing and basic amenities. Another 80 workers are in
Cod Bay, Trincomalee where the floating craft are stationed.
LTTE agents
It is an open secret that there are LTTE agents or sympathisers
among the staff on the site. The rebels, however, never made any
attempt to destroy the plant. They only disrupted production by
blasting the Yan Oya fresh water supply plant and put an end to
bulk shipments by attacks on merchant shipping.
The LTTE had
previously warned merchant shipping to stay away on the grounds
that it considered the mineral wealth on the shores of Pulmoddai
to be part of the natural resources of their "homeland"
and an important source of foreign exchange for their projected
separate state.
Conditions
at the Pulmoddai plant have improved since the cease-fire came into
effect. The nearby town - hardly more than a sleepy village - bustles
when dozens of lorries come from Colombo and Negombo to collect
fish.
Fishermen can
go out to sea now that the ban on fishing has been relaxed under
the terms of the Memorandum of Understanding between the government
and the LTTE. At night, a string of lights from fishing craft can
be seen on the horizon. Sea Tiger craft have been seen speeding
past, hugging the coast.
Bulk shipments
of ilmenite ceased in September 1997 when Sea Tigers sank the bulk
carrier, M.V. Cordiality. By then the company's godowns were full
and it had stopped producing heavy minerals, there being no place
to store the product. The ship was supposed to carry 30,000 tonnes
of ilmenite to Europe. "We had filled the holds with 29,000
tonnes of ilmenite worth Rs. 90 million and were expecting to finish
loading within another 10 hours when the ship was attacked,"
recalled Nandadeva.
Midnight
strike
Sea Tigers struck shortly after midnight. Nandadeva was woken
up by a telephone call from the jetty and was told that firing could
be heard from the ship which was anchored about a mile offshore.
Navy boats had been patrolling the waters near the vessel and sailors
dropping grenades into the water to deter LTTE scuba divers.
"From
my bungalow I could see the ship. There were no lights except for
one on the mast. Usually the ship is lit up like a small town."
Five minutes
later he saw a flash - a huge fireball - and then heard the blast.
Later he found that the Tigers had boarded the vessel, entered the
captain's cabin and told him to evacuate the ship's crew as well
as the stevedores - there had been 60 casual labourers on board
- saying that they had planted explosives in the vessel. The chief
engineer and four crew members who were down in the engine room,
were killed along with eight employees of the company and six soldiers
guarding the vessel. The vessel continued to burn into the next
day. The wreck can still be seen, its cranes sticking out of the
water. The company wants to clear the wreck to make way for shipments
to resume.
The company
was originally called Ceylon Mineral Sands Corporation and was set
up under an act of parliament in 1957. The first shipment of ilmenite
went to Ishihara Sangyo Kaisha Ltd of Japan in 1962. There is even
a road at the site named Ishihara, which makes titanium pigment
and helped set up the plant. In 1976 an integrated ilmenite/rutile/zircon
plant was built at Pulmoddai to process all products.
A lifetime
spent with Lanka Mineral Sands
Muhammad
Nassar, chairman of Lanka Mineral Sands, refers to the company's
general manager S.A. Nandadeva as the father of the mineral sands
plant.
Nandadeva joined
as a graduate trainee in 1969 and stayed on site even during the
worst of times, when many others left. He studied mining and minerals
processing engineering in England and went to Australia for practical
training. "At the time it was a very small plant - processing
only ilmenite - with a capacity of 40,000 tonnes," Nandadeva
recalled. He rose through the ranks, becoming mining engineer, assistant
plant manager, project engineer, plant manager and finally general
manager in 1986.
One of the
memorable incidents he recalled during his time at the site was
when the Yan Oya water supply plant was attacked by the LTTE in
1986. None of the 30 employees at the site was harmed. Nandadeva
and several others went on bicycles to the site and found staff
hiding in the jungle. Later, an elderly villager told him that the
LTTE had noted him. On another visit to Yan Oya he was stopped and
questioned by the LTTE.
Nandadeva said
resident staff has always lived in hope that things would get better.
Before the outbreak of the Eelam war, and even during the war years,
workers enjoyed good pay and bonuses as mineral shipments invariably
generated healthy profits. But many qualified and skilled people
left the plant as the war dragged on, conditions deteriorated and
finally production ceased.
Nandadeva said
he stuck it out at Pulmoddai because of the commitment he had towards
his work, fellow workers and the company. "I was fortunate
to receive a lot of training and was given many responsibilities,"
he said. "I would not otherwise have got such opportunities."
He turned down
offers of two jobs and stayed on at the plant despite the objections
of his wife because of what he felt were his obligations to the
company.
Having spent
a lifetime at Pulmoddai - more than 30 years - Nandadeva looks forward
to the day when the company makes value-added products instead of
just shipping minerals sand in bulk. "My dream is to make synthetic
rutile - an upgraded feedstock that is much in demand," he
said, adding that the company wants to get into a joint venture
with a technology provider.
|