Making brushes with
care and perfection - Special facilities for handicapped workers
at Harris
By Sachini Perera
Ever wondered how a paint brush is made or that
brush making has become a craft that is being passed on from generation
to generation?
Well, these are some of the amazing facts that
were learnt during a visit to the factory of Harris
Ceylon Limited, located at Meegoda.
It was as far back as 1935 that Sri Lankans were
first introduced to Harris brushes when W.D. Carolis began to import
them from L.G. Harris Ltd in the United Kingdom. Undaunted by the
import ban of 1969, he set up Harris Ceylon Ltd in conjunction with
the mother company in the UK. His successors were C.G.D. Carolis
and Michael Dias, father of the present Managing Director Sujan
Dias.
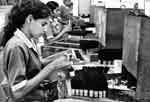 |
A selection of the 125 staff who work at the
Harris Ceylon's brush factory located at Meegoda. |
For nearly 40 years, Harris has gradually worked
at establishing itself in Sri Lanka. Now the company is a household
name synonymous with paint brushes. On hindsight, the decision W.
D. Carolis made has proven to be invaluable given that only a handful
of other countries (China and Kenya) have the privilege of manufacturing
Harris brushes. It has given Sri Lankans the chance to purchase
these brushes at affordable prices and also to be part of a great
industry.
A tour of the Harris factory, starting outside,
at the sheds with wooden planks used to make handles and finishing
off at the stores, from where the finished product is distributed,
gives one a good idea as to what goes into the production of a paint
brush. “We believe in maintaining our quality and therefore
it is all done under one roof, without outsourcing,” said
Narada Amaratunga, Production Manager at Harris Ceylon Ltd.
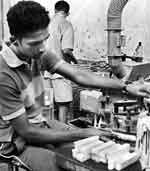 |
Staff who work at the Harris Ceylon's brush
factory |
In fact, the rubber wood treated with chemicals
is the only thing that is outsourced in this factory. While their
primary provider is Panawatta Plantations belonging to the Hayleys
group, there are other suppliers as well. It is ensured that all
wood planks used at the factory are up to the standard maintained
by Harris brushes internationally. As you enter the factory the
loud roar of the huge cutting machine greets you.
It is these cutting machines that cut the planks
to make brush handles of different sizes. And following these, all
you see, up to the other end of the building are various machines
that contribute at different stages of the production process. “Ninety
per cent of these machines are imported, mainly from the UK and
at least 80 per cent of the production process has been automated,”
said Amaratunga, barely audible over the racket of one machine trying
to outdo the other.
Each machine is supervised by the factory staff
who keeps a close watch over the metal beasts.
The raw handles are sent through the sanding machine
and varnished and painted with the trademark colours of Harris,
the familiar red and white.
Then the handles are stamped with the Harris logo.
Amaratunga noted that the stamp and the paint cannot be duplicated
because they come from the mother company in the UK. Although the
paint used was said to be environmental friendly, the workers wore
masks for extra precaution.
In addition to paint brushes, wire brushes are
also manufactured but with the high demand there is to be met in
the case of paint brushes, the factory tends to concentrate more
on them than any other brushes. They work according to a monthly
production forecast.
In addition to the automated brush making and
assembling process, there is something very interesting going on;
manual brush making.
The manual brush makers are a select group of
veterans of the craft, about five or six people out of the 125 factory
workers. Their efficiency is evident in their workmanship. One reason
for manual brush making is that some of the sizes cannot be made
by the machines. But most importantly, to most workers at Harris
Ceylon Ltd, brush making is a tradition. It has been passed on from
mothers to daughters and at this juncture, an interesting observation
could be made.
The administration of Harris Ceylon has come down
from generation to generation and most employees have also followed
suit. As most employees are from the town of Meegoda, for them,
it is a craft rather than a mere job. Therefore, you see different
generations from families working in unison, with trade secrets
being passed down from mother to daughter.
“It is like a family and it is very good
to work here,” said Rozanna De Alwis, a Supervisor at the
factory. Her loyalty to the company is apparent because she started
working for the company as a 19-year old in 1968, and after being
abroad for a few years she once again returned to Harris. She has
no regrets about it and calls it “the best place you can work
at.”
Another outstanding attribute is that even supervisors
like her were seen working together with the staff on the same level,
proving De Alwis’s words that they are a family unit.
The highlight of the production process is what
you could call Harris’ secret formula. It is a special glue
that guarantees against bristle loss. This is an advantage that
Harris Ceylon Ltd has because they received technical know how from
the mother company.
The bristles are imported from China. Although
Harris is marketing synthetic bristled brushes such as the new No
Loss range, they are still not manufactured in the factory. Next,
the brushes are put through trimming and during this any loose bristles
are removed.
These waste bristles are not thrown away. There’s
another machine called the turning machine in which collected waste
bristles are turned and readied to be re-used.
The handles and bristle heads are joined manually
and they are rammed together by nailing or stapling, depending on
the type of brush. Then the finishing touches are added by cutting
the odd pieces off and by combing through the bristles to check
for bristle loss one last time. Another group of veterans perform
a task known as quality check. Their job is to spot any shortcoming
the brushes may have which would prevent them from reaching the
international standard Harris aims at. It is fascinating to watch
their ability to spot a flaw at a glance. Despite the high local
demand, the brushes made in Sri Lanka are exported to the UK, the
Middle East, Maldives and Hong Kong.
Currently there’s a blind couple and also
a blind young man working for the packing section. It is part of
the company policy to help the community. There are steel railings
in the factory, including the lavatories for the blind workers to
find their way around the premises. The factory also helps maintain
the train station that runs right in front of the factory and looks
after the needs of the staff such as medical requirements and transport.
The factory of Harris Ceylon Ltd shows that the
driving force behind its success is the employees whose loyalty
to the factory as well as the craft of brush making is obvious.
Disna Damayanthi, who was multi-faceted, not only at brush making
but also at working and talking at the same time said, “We
are treated very well and in return, we do our part”.
These sentiments were reflected in the words of
the company’s Managing Director Sujan Dias. “To be able
to produce a product of that high quality, you have to be genuinely
interested in what you are doing.”
Harris Ceylon Ltd shows that in today’s
business oriented culture, there are factories where there is good
rapport between the employers and the employees and genuine interest
in the product they are manufacturing.
|