Peek into Asia’s
best garment washing plants
By Lakwimashi Perera
Ever wondered how a brand new pair of jeans is
made to look worn and scruffy even before it reaches the seller
or how a boring white t-shirt is transformed into a colourful garment?
The Sunday Times FT got a chance to visit Brandix Finishing’s
Ratmalana facility and find out exactly how this happens.
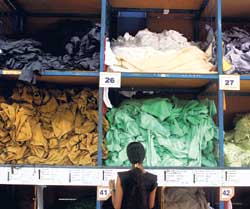 |
A worker ponders at the 'load' for washing.
Pic. By J.Weerasekera |
Brandix Finishing Ltd which started with 15 wash
machines has, over the last 10 years grown into one of the largest
players in the field of garment washing, dyeing and finishing –
not only in Sri Lanka but the whole of Asia.
The Ratmalana facility offers such services as
washing, dyeing with special finishes such as grinding and sandblasting
also on offer while another Brandix facility at Avissawella mainly
focuses on garment dyeing at the moment, says Felix Dias Abeyesinghe,
Manager – Marketing & Merchandising. The Ratmalana plant
provides employment to about 1500 workers with the Avissawella plant
employing close to 600. The clientele of Brandix Finishing include
giants in the international market such as Abercrombie and Fitch,
Gap, Victoria’s Secret, Marks and Spencer, Next, Dockers,
Levi’s, Diesel to name a few. The optimum balance, according
to Abeyesinghe, would be a 50-50 split between the American and
UK customer, but this varies with each season.
The receiving bay is where the journey began,
with all garments that need to be washed, dyed and finished being
brought there. The garments, brought there by customers within the
Brandix group as well as non-group customers, are stored according
to the process that it needs to undergo. Here the daily allocations
are made for the washes.
From the receiving bay it’s on to the pre-wash
inspection area where each load that comes is inspected on a random
basis. “This is to make sure that the garments that we have
here are suitable for washing,” Abeyesinghe told us. Depending
on the product, what has to be done to the garment before it is
washed will be recommended to the customer. The pre-wash colour
standard is also checked. Once these are checked and the inspection
is successful, the garments are sent for washing. If the inspection
fails the garments are put on hold while the customer is advised.
Confirmation from the customer will send the garments on their way
to be washed. If no confirmation is received the garments are returned.
The decision has to come from the customer.
Brandix Finishing boasts of the largest sampling
facility in Sri Lanka which will be officially opened in the coming
month. Explaining the importance of sampling, Abeyesinghe said,
“When a buyer confirms an order the bulk order is not produced
immediately. There are different stages of sampling that we have
to go through before we hit the bulk stage. Looking at the samples
the buyer will decide what they want to do in the final bulk ranges.
Today customers decide on orders based on sampling turnaround and
sample approvals. If we don’t get the samples right there
is no bulk order.”
After sampling comes the dyeing stage. “Our
strength lies mainly in garment dyeing. We as a finishing house
concentrate on garment dyeing and special finishes,” he explained.
After a garment is dyed it is sent to the washing machines to be
washed. Here the garments undergo washes such as enzyme washes,
stone washes, bleach washes etc. After washing the garments are
sent to the dryers for drying after the water is extracted from
them.
Brandix Finishing is also home to the biggest
laser facility in Asia, where any kind of garment, ranging from
children to adults, from pants to shirts, could be finished. Laser
technology replaces the old technology of sandblasting. Laser technology
is preferred by the customers as the accuracy is higher, and the
fall-out rate is lower as it is computerized. Laser technology is
also more environmentally-friendly when compared to sandblasting.
Processes like grinding, curing, hand-sanding,
spraying, tying, painting also known as the special finishes are
done in a separate area. The manual work done here is what most
customers require and it is what adds value to the garment. Majority
of the work force is involved in these manual processes. Grinding
is the process where garments such as jeans are made to look old
and worn by shredding the ends. “It is a risky job involving
a lot of skill and talent and adds a lot of value to the garment,”
Abeyesinghe noted, adding that the workforce that is employed in
that area are all permanent workers who are constantly trained in
these skills. Having a large workforce engaged in manual finishes
is what the customers are looking for. Brandix Finishing has an
in house multi-skill programme where employees acquire more than
one skill, which also helps the company to retain people.
The final quality inspection area is where the
final inspection before dispatch takes place. A 100% inspection
is done here before handing over to the customer. If the garment
does not meet the requirements of the customer it is sent back for
re-processing.
The final stop for a garment that had been through
Brandix Finishing is the final dispatch area, where it will arrive
after the washing, dyeing, finishing and inspection. When the garments
are ready for dispatch, the customer, on collection is required
to count simultaneously with a Brandix Finishing representative,
so as to avoid any conflict in the numbers.
Throughout the tour it was obvious that large
amounts of water were being consumed by the facility. Since we found
out what happens to the garments since their arrival at the plant,
we were also keen to find out the fate of the water that is used.
Hilary Thiagarajah, Manager – Environment
Research Engineering showed us around the waste water treatment
plant at Brandix Finishing which treats the water that is contaminated
in the washing, dyeing and finishing of garments. Water coming from
the wet processes are treated in three stages, the first being the
physical treatment which is also the primary treatment. Here the
water is allowed to settle in a tank where all the suspended matter
settles.
Thereafter it goes to the equalisation tank. Here,
water coming from different processes (and therefore, containing
different effluents such as softener, bleach, dye etc) are mixed
together with defused air. This stage is called homogenisation.
Next is the biological treatment phase where microbes
are allowed to grow in the water. Nutrients are added to the physically
treated water to help the growth of the microbes and the temperature
is also controlled to ensure the optimum temperature for microbial
growth. Air is also pumped into the water. These microbes digest
the chemicals in the water and die in the process. The dead microbes
float on water creating the biological sludge which looks a lot
like a dirty soapy scum on the water. A scraping arm rotating around
the tank removes the sludge from the surface of the water sending
the water to the third and final stage of its treatment, the chemical
treatment.
Thereafter, chemicals are added to the water and
it is sent to the DAF (Dissolved Air Floatation) unit. Here another
sludge is formed and again, defused air brings the sludge to the
surface. A rotor, which is a more advanced and faster method of
sludge removal, gets rid of the surface sludge.
The water that finally comes out is clear and
most of it is released to the drainage system, finally reaching
the Lunawa lagoon, with about 10%-20% being retained for re-use
within the facility.
According to Thiagarajah, research has shown that
the sludge is high on nutrients and has a fertilizer value. “We’re
planning on using this as a fertilizer,” he said. He pointed
out that a research study that is being carried out with a student
of the Moratuwa University shows that a mixture of sludge and soil,
mixed at a particular ratio, promotes the growth of plants more
than normal soil alone does.
The primary sludge is also mixed with cement and
turned into cement blocks that can be used for construction work.
This is also an ongoing research project.
With environmental pollution on the rise and its
adverse effects on man and nature becoming more and more harmful,
it is a welcome change to see companies such as Brandix Finishing
trying to minimize the impact they have on nature while also maintaining
the quality and standards that give them the edge in the national
and international market.
|