Lean office is a workplace where all business transactions take place Right the First Time (RFT) using lowest possible resources. It is simply a place of doing more with less. Implementing lean in an office environment is not that easy as the rate of change in the voice of the customer in a service environment is very much higher than that of manufacturing environment.
Some of the factors to be considered in making a lean office are briefed below for the knowledge of service providers.
1. Office Automation
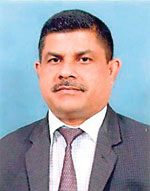 |
Mr DMA Kulasooriya |
If you automate a wasteful process, what you end up with is automated waste. Computers are found everywhere in non-factory environments, but they are only as effective as the processes set in place to facilitate their use. Lean processes consume less stationery, less energy and less time to provide an error free service.
Moreover, service delivery processes are made of a few customer contact points (CCP) with an appropriate technology and the simplest method. Automation is to be done purely with the purpose of reducing the time taken to complete a process and reducing errors or mistakes in a given process.
2. Elimination of Waste
Eliminating waste allows value to flow with higher speed and quality through the business process. This idea is central to the Lean office approach. Waste is anything that does not add value to a product or service. Simply put, it is anything for which the customer would not be willing to pay. Some forms of waste appear obvious; others may be latent or intangible.
- Information waste
- Process waste
- Waste in the physical environment
- People waste (i.e., inefficiencies in how people work)
3. Lead Time Reduction
Office processes account for up to 80% of the lead-time in many manufacturing and service industries. The results of waste in the office-such as delayed response to customer orders or incorrect accounting-can be costly and often devastating. Thus, purging the office of wastes hastens the journey toward the Lean office: cost-effectiveness, customer satisfaction, and profitability.
How to make a lean office
Step 1: Mapping the Value Stream in the Office
Value-stream mapping provides a unifying plan that helps focus your Lean office efforts on the process issues that most impact your organization's strategic intentions. Implementing the Lean office requires investment and organizational commitment. Expending these resources and energy in a haphazard manner without a clear sense of direction is wasteful and counterproductive.
Step 2: Preparing for a Kaizen in the Office
In any intervention, adequate preparation is crucial for ensuring a successful outcome. In detail, the five preparatory activities help enhance the success of your Lean office kaizen event. Those activities are listed below.
- evaluating the situation
- developing a charter
- gathering data
- updating the charter
- planning for the kaizen
Step 3: Conducting a Kaizen in the Office
With the preparation in place, you are now ready to have a kaizen in the office. From the beginning kick-off to the final report-out; kaizen workshops can be exciting and productive for everyone involved. No matter what the outcome, it is a valuable learning experience and an opportunity for team development.
|