The principles of Lean Thinking have gone well beyond the factory floor. With the rise of more consumer - provider services, the service industry is quite ripe and in need of the principles of Lean Thinking.
In an article back in 2005, Womack and Jones expand the principles of Lean Thinking in an article published in the Harvard Business Review (HBR) as "Lean Consumption".
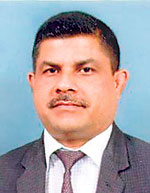
DMA Kulasooriya |
Lean Consumption "minimizes customers' time and effort by delivering exactly what they want when and where they want it". Processes are focused on eliminating waste, while increasing productivity, speed of operation and improving customer interaction.
Principles of Lean Consumption
- Solve the customer's problem completely by ensuring that all the goods and services work, and work together.
- Don't waste the customer's time.
- Provide exactly what the customer wants.
- Provide what's wanted exactly where it's wanted.
- Provide what's wanted where it's wanted exactly when it's wanted.
- nContinually aggregate solutions to reduce the customer's time and hassle.
None of these focus on specific attributes of a product. Today the product is not the major problem. Problem is the time line of service or manufacturing process which consumes the materials and the time
Methodology
Making a business process lean means reducing consumption of materials and time. More conversely it is an effort to reduce consumption of materials and time along the time line from the moment the customer gives us an order to the point when we collect the cash. Question is what and how are the methods of shortening the time line. This can only be done by removing the non-value added wastes. Today Lean Management System provides many a solution to this effect.
- Identify and improve activities that create and add value for the customer.
- Determine what processes are necessary to deliver that value.
- Cut down on activities that do not add value.
- Deliver products precisely when the customer requires them.
- Improve and streamline these processes continuously.
As lean thinking continues to spread to every country in the world, business leaders are also adapting the tools and principles beyond manufacturing, to logistics and distribution, services, retail, healthcare, construction, maintenance, and even government. Indeed, lean consciousness and methods are only beginning to take root among senior managers and leaders in all sectors today.
What is Kaizen?
Kaizen is actually a "way of life philosophy," assuming that every aspect of our life deserves to be constantly improved. The Kaizen method of continuous incremental improvements is originally a Japanese management concept for incremental (gradual, continual) change (improvement). The Kaizen philosophy lies behind many Japanese management concepts such as Total Quality Control, Just-in-Time/Sequencing (JIT/S) and Lean Manufacturing. Key elements of Kaizen are quality, effort, involvement of all employees, willingness to change and communication - DMAK |